McCauley Wycliff
Member
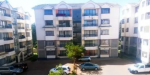
Kenyans are leveraging on new alternative building technology in order to bring the cost of building houses down to a level that can be deemed as affordable.
Advanced countries have solved their housing challenges through the use of new cutting-edge technology.
Government data indicates that Kenya has a housing deficit of approximately two million units, while more than half of urban residents live in informal slums.
This has occasioned the rapid adaptation of the latest construction automation techniques.
Here's a look at 5 techniques Kenyans are employing to save on construction costs.
Insulating concrete formwork (ICF) technique
ICF building systems comprise large polystyrene blocks that lock together to form a house-shaped mould into which concrete is poured to form the wall structure of your ICF house.
Each polystyrene block comprises two pieces of insulation joined together by metal straps.
Once assembled together with all the other ICF blocks they form an inner wall of insulation and an outer wall of insulation with a void in between where the concrete will eventually go.
When all the ICF blocks are joined together they look just like a traditional cavity wall made from polystyrene.
Once assembled the walls are supported with shuttering before the void (or cavity) is filled with concrete to form the wall structure.
National Housing Corportaionworkers construct a sample EPS panels house in Nairobi.
According to the state department of public works, there are a number of companies that are locally manufacturing Expanded Polystyrene (EPS) panels
Precast foundation technique
This is an off-site construction technique in which the foundation units are pre-engineered and manufactured in a controlled environment.
These units as are pre-engineered, their capacities or limits are communicated with the purchaser to produce the desired unit.
The precast concrete foundation units are stronger and lighter when compared to other competing materials.
This method reduces the overall cost of building a house.
Thin joint masonry technique
Described as an innovative construction method for use with aircrete blockwork, this method allows build times to be significantly improved and offers many other practical and commercial benefits.
Independent tests have shown that by using this method, a team of skilled tradesmen with no prior 'thin joint' experience can build the Inner leaf of a detached, 4-bedroomed, 2-storey house in just five to six days.
Precast flat panel modules
This is a construction technique that provides an alternative to traditional site-based construction.
Precast flat panel system components are mass-produced off-site, making them practical for recurring requirements that also demand speed of manufacturing and consistency of product.
Panels can include elements, such as doors, windows, and floor units. They can also include features such as decorative wall finishes and fitted insulation.
Flat slab technology
This technique utilises flat slabs (reinforced concrete slab held directly by concrete columns without the use of beams) to facilitate easy and quick insertion of horizontal features and for the partitioning of buildings.
It is ideal for most construction projects and for asymmetrical column layouts such as floors with curved shapes and ramps.
The flat slab technique is easily one of the quickest construction methods available.
In addition, it helps to significantly cut down labour costs by reducing reinforcement requirements
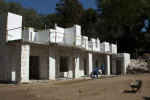
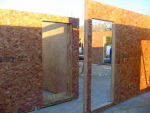